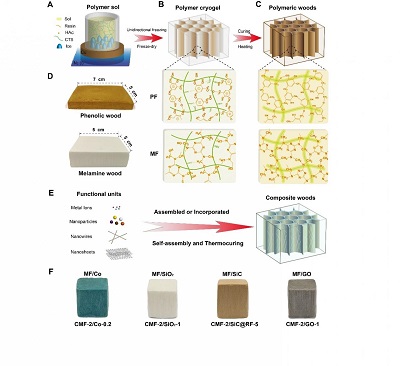
INTRODUCTION
Nature has been a supply of bioinspiration for supplies scientists within the design of high-performance engineering supplies (1–Four). Wooden, as one of the widespread pure supplies, has attracted huge consideration attributable to its light-weight and high-strength properties. An intensive evaluation of wooden constructions and an understanding of structure-function relationships are very enlightening to engineering (5, 6). The distinctive hierarchical mobile construction and matrix (lignin and hemicelluloses) embedded with well-oriented cellulose fibrils endow the wooden with admirable mechanical properties. Wooden grows by a biologically managed bottom-up self-assembly, and each structural stage contributes to the outstanding properties of wooden, together with the mechanical properties in addition to the multifunctional and adaptive properties (7).
As understanding of wooden construction deserves deep consideration, many wood-inspired superior supplies have been designed utilizing “top-down” or “bottom-up” methods. Not too long ago, numerous wood-derived composite supplies with superb performances are fabricated by modifying the microstructure of the pure woods such because the superb “tremendous wooden” or combining wood-derived cellulose with artificial supplies (eight–10). The wood-derived supplies have intrinsic excellent benefits, comparable to renewability, biodegradability, wonderful toughness, and the likelihood for novel functionalities (10). The low-cost and plentiful uncooked supplies additionally present a adequate supply for the high-performance wood-derived supplies with promising functions. Nonetheless, it's nonetheless a problem for wood-derived supplies to beat the drawbacks of wooden, comparable to inflammability and poor corrosion resistance.
A bottom-up technique is one other doable route for fabrication of wood-like monoliths through the use of polymer because the matrix and micro- or nanoscale supplies because the constructing blocks, comparable to freeze-casting and three-dimensional (3D) printing (11). Nonetheless, the standard wood-like supplies together with mobile polymer supplies and mobile ceramic supplies are restricted by the unsatisfactory mechanical performances and poor controllability (12, 13). Most ceramic-based, wood-like supplies are made utilizing ceramic powders, adopted by an ultrahigh-temperature sintering normally above 1500°C to combine the powders right into a full monolith (14–16). 3D printing can also be another technique to fabricate mobile supplies or inerratic honeycomb constructions; nevertheless, it's nonetheless a problem to make macroscopic bulks with micrometer-sized constructions (12).
Right here, impressed by wooden, we report a brand new method for bulk synthesis of a household of synthetic polymeric woods with lifelike look and mobile constructions by the low-temperature curing of predesigned polymeric matrices (Fig. 1, A to D). This time-efficient technique contrasts strikingly with the a long time or a whole bunch of years wanted to develop pure wooden. Our synthetic woods exhibit not solely good controllability in microstructures but in addition comparable mechanical properties with these of pure wooden. Additional, in distinction to pure wooden, they show preferable corrosion resistance to humidity and acid with no lower in mechanical properties, in addition to a lot better thermal insulation (as little as ~21 mW m−1 Ok−1) and fireplace retardancy. The polymeric woods stand out even from different engineering supplies comparable to mobile ceramic supplies and aerogel-like supplies by way of particular power and thermal insulation properties. They present promise to be used as novel biomimetic engineering supplies and an alternative choice to the pure wooden.
Fig. 1 Fabrication scheme of the bioinspired polymeric woods and sorts of composite woods primarily based on PF and MF.
(A) Beginning answer (sol) together with water-soluble thermoset resins, CTS, and acetic acid (HAc), forming a homogeneous polymer answer. (B) Predesigned matrix ready by the ice template–induced self-assembly and freeze-drying course of. (C) Ultimate polymeric woods after thermocuring the predesigned matrix. The resins are fully cross-linked. (D) Pictures of the unreal polymeric woods primarily based on phenolic resin (high, mobile CPF-Four-5) and melamine resin (backside, CMF-Three-5). (E) Scheme illustration displaying the fabrication of varied composite woods by including ions or purposeful nanomaterials into the polymer answer, adopted by the above self-assembly and thermocuring course of. (F) Pictures of varied composite woods primarily based on melamine resin, together with MF/Co (CMF-2/Co-Zero.2), MF/SiO2 (CMF-2/SiO2-1), MF/SiC (CMF-2/SiC@RF-5), and MF/GO (CMF-2/GO-1). Dimension of the composite woods, ~1 cm × 1 cm × 1 cm.
RESULTS
Materials synthesis and characterization
As a matrix substance of pure wooden, lignin is a sort of amorphous polyphenol and not using a well-defined major construction and could be described as a “chemical internet,” which glues cellulose fibrils (fig. S1A) (17). Resol, a sort of water-soluble liquid phenol-formaldehyde resin (PF) with an analogous amorphous polyphenol construction, is used because the substitute matrix (Fig. 1B and fig. S1B). The synthetic polymeric wooden is fabricated by curing the predesigned resin matrix. The hierarchical mobile constructions are generated by a unidirectional ice crystal–induced self-assembly course of. A small amount of chitosan (CTS) performs a key function as a brief scaffold to assist the mobile construction and overcome the resins’ creep deformation after ice sublimation by the use of the robust interplay between the amino teams and the hydroxymethyl teams (18). The water-soluble melamine-formaldehyde resin (MF) can also be matrix candidate attributable to its numerous hydroxymethyls (Fig. 1B and fig. S1C). The polymeric PF- and MF-based woods with good mobile constructions are accomplished by a subsequent curing course of at temperatures not greater than 200°C (Fig. 1, C and D). Moreover, attributable to good compatibility, the current method for polymeric woods supplies a brand new and highly effective path to fabricate multifunctional composite mobile supplies, and nearly all of the water-soluble molecules or water-dispersed nanomaterials, comparable to metallic ions, nanoparticles, nanowires, and nanosheets, could be assembled or included into the polymeric woods to type composite woods with completely different appearances and properties (Fig. 1, E and F). The ready mobile polymeric woods are named CPF-x1-y or CMF-x2-y, the place x1 = 1 to five and x2 = 1 to three correspond to the incremental resin content material within the answer (desk S1), and y corresponds to the freezing charge. As an illustration, CPF-1-5 and CPF-Four-5 are consultant of the mobile PF wooden ready through the use of Three.6 weight % (wt %) and 14.5 wt % resol slurry, respectively, at a freezing charge of 5°C min−1. The composite woods are labeled as CPF-x/Filler-z and CMF-x/Filler-z, the place z denotes the focus (in milligrams per milliliter for nanomaterials and in moles per milliliter for ions or micromolecules) of fillers within the answer.
Wooden, comparable to balsa, consists of parallel hole tubes with a cell measurement of about 50 μm and a wall thickness of about 1 μm (Fig. 2, A to C). Through the use of the amorphous PF resin and MF resin because the matrix, we efficiently made the macroscopic CPF and CMF woods. As demonstrated by scanning electron microscopy (SEM) pictures of the cross part and longitudinal part, the everyday CPF wooden consists of parallel hole tubes with a pore measurement of ~50 μm and a wall thickness of three to five μm (Fig. 2, D to F). The macroscopic CMF wooden will also be fabricated with 30- to 40-μm parallel tubes (Fig. 2, G and H). The CMF wooden (CMF-Three-5) displays distinctive fishbone constructions with interconnected channels (Fig. 2I). The fishbone morphology outcomes from the facet branches as a result of secondary instability formation perpendicular to the freezing course when the viscous MF polymers focus across the major stable ice cell (19). The multifunctionality of the polymeric woods could be realized by compositing purposeful nanomaterials comparable to graphene oxide (GO) to the polymer answer (Fig. 2J). The PF/GO composite wooden (CPF-1/GO-1) with a low density of ~85 mg cm−Three manifests a pore measurement of ~50 μm and a wall thickness of ~2 μm, and GO is tightly connected to the partitions (Fig. 2, Ok and L). X-ray microtomography of a typical CPF-Four-5 revealed the flawless mobile constructions with tubes parallel to the freezing course all through the fabric (Fig. 2M and film S1). As to the composite woods, the resin serves as a glue to assemble nanomaterials collectively, with the fillers dispersed homogeneously within the ultimate mobile supplies, resulting in numerous visible traits and homogeneous microstructures (fig. S2). Moreover, large-scale fabrication with completely different sizes for all these sorts of polymeric woods could be simply achieved as a result of cost-effective uncooked supplies and the straightforward fabrication course of (Fig. 1, D to F, and fig. S3).
Fig. 2 The structural characterization of the balsa and polymeric woods.
(A) Balsa wooden with a density of ~90 mg cm−Three. (B and C) SEM pictures of the cross part (perpendicular to the channel course) and the longitudinal part (parallel to the channel course) of the balsa wooden. (D) Synthetic CPF wooden (CPF-Four-5) with a density of ~280 mg cm−Three. (E and F) SEM pictures of the cross part and the longitudinal part of the CPF wooden. (G) Synthetic CMF wooden (CMF-Three-5) with a density of ~560 mg cm−Three. (H and I) SEM pictures of the cross part and the longitudinal part of the CMF wooden. (J) PF/GO composite wooden (CPF-1/GO-1) with a density of ~85 mg cm−Three. (Ok and L) SEM pictures of the cross part and the longitudinal part of the PF/GO composite wooden. The inset in (L) exhibits the enlarged picture of the node of the partitions. (M) 3D reconstruction of the CPF wooden (CPF-Four-5) derived from x-ray microtomography, and microtomography pictures show the straight, parallel tubular pores. Sale bars, 200 μm.
The pore measurement and the wall thickness of pure woods are affected by many elements, comparable to wooden species and local weather. The mobile constructions created by ice templating will also be tuned by parameters comparable to polymer focus, freezing charge, and curing temperature. To precisely management the freezing charge, we designed a do-it-yourself instrument with a temperature controller (fig. S4). The channel measurement strongly relies on the resin content material and the freezing charge. A sluggish freezing charge permits the formation of bigger pores by the big ice crystals, and a quick freezing charge leads to smaller channels as a result of the supercooling impedes the formation of huge ice crystals (20). As well as, excessive polymer focus promotes the formation of small ice crystals and vice versa (20, 21). In correspondence with the above guidelines, the pores grow to be smaller and the partitions grow to be thicker because the resol content material will increase or the freezing charge will increase (fig. S5). To quantitatively assess pore measurement and wall thickness adjustments, we decided the statistical space and wall thickness distributions primarily based on the cross-section pictures. A sooner freezing charge and a better resol content material enable narrower distributions of each the pore measurement and the wall thickness (figs. S6 and S7). The uncontrollable shrinkage of polymer cryogels in the course of the curing course of additionally barely influences the pore constructions and wall thicknesses (figs. S8 to S10). Because the freezing charge will increase from 1 to 10°C min−1, the typical pore measurement (space) of all CPF samples decreases sharply from 3000 to 6000 μm2 to 500 to 2000 μm2, and the typical wall thickness decreases from Four to eight μm to 1 to five μm (fig. S11, A and B), whereas the curing temperature exhibits a slight affect on pore measurement and wall thickness (fig. S11, C and D). Equally, a sooner freezing charge and a better polymer focus create smaller pores for CMF woods with apparent fishbone construction as a result of excessive viscosity of the MF answer (fig. S12). Except acknowledged in any other case, we fabricated polymeric and composite woods at a freezing charge of 5°C min−1 and curing at 180°C. On this method, a household of polymeric woods could be fabricated with well-controlled obvious densities (90 to 600 mg cm−Three) and porosities (40 to 90%) (fig. S13).
Mechanical performances and failure mechanism
The low density and excessive power of pure woods are essentially the most fascinating benefits that entice appreciable analysis consideration. Two sorts of polymeric woods manifest very excessive compressive power and elastic modulus alongside the axial course as a result of anisotropically honeycomb-like microstructures, for instance, the compressive yield strengths of CPF-5-10 and CMF-Three-5 can obtain ~35 and ~45 MPa and the elastic moduli obtain ~700 and ~653 MPa, respectively (Fig. 3A). Most engineered mobile supplies present a scaling relationship of σ/σs ~ (ρ/ρs)n between yield power (σ) and density (ρ) and E/Es ~ (ρ/ρs)n between Younger’s modulus (E) and density, the place σs, Es, and ρs denote the power, modulus, and density of the corresponding stable constituent materials, respectively (22). The ability n of the scaling relationship relies on the fabric microarchitecture. For instance, mobile supplies with stochastic porosity exhibit the relative elastic modulus scaling with n = 2 or Three (22). Typically, the honeycombs are very robust and stiff when loaded within the out-of-plane compression (axial course) (16). The linear elastic regime is truncated by structural buckling, and the supplies lastly failed by tearing or crushing. The relative power and modulus for a great honeycomb construction with common hexagons and uniform wall thickness, which observe the plastic buckling, scale as σ/σs ~ (ρ/ρs)2 and E/Es ~ ρ/ρs from the analytic prediction (23). Beneath axial compression loading, the relative yield power and relative modulus of CPF supplies show roughly quadratic scaling relationships: σ/σs ~ (ρ/ρs)2.1 and E/Es ~ (ρ/ρs)1.eight (Fig. 3B), demonstrating an open-cell structural bending fracture–dominated conduct, the place the fracture occurs predominantly by the failure of cell partitions (22). Such a deviation from the theoretical prediction could be defined by defects and structural imperfections. The ability n of scaling legislation between the yield power and density, in addition to the compressive modulus and density of the polymeric woods, was affected by the freezing charge and curing temperature (figs. S14 to S16) in experiments. A sooner freezing charge creates extra compact and common constructions, leading to greater strengths and moduli. Excessive temperature facilitates extremely cross-linked resin networks, thus producing greater modulus. The irregular polymeric woods with incompletely cured partitions ready by sluggish freezing charge (1°C min−1) and low curing temperature (160°C) exhibit excessive scaling energy of the elastic modulus (n ≈ 2). Typically, for the comparatively common polymeric woods (freezing charge, >1°C min−1) with fully cured partitions (curing temperature, >160°C), the yield power of the polymeric woods varies roughly as ρ2, whereas the Younger’s modulus varies roughly as ρ1.6, demonstrating a bending-dominated failure mode of open-cell constructions (Fig. 3C and fig. S17).
Fig. Three Compressive performances and failure mechanisms of the polymeric woods.
(A) Axial compressive stress-strain curves of typical polymeric woods. (B) Relative power and modulus as capabilities of the relative density of CPF woods. (C) Ashby chart plotting compressive yield power versus density for polymeric woods and different engineered supplies, together with solid resin (14), SiC foam (15), 3D-printed honeycomb (14), mullite-ZrO2 foam (16), PF carbon foam (24), and RF aerogel (25). Symbols ‖ and ⊥ symbolize the compressive instructions which can be parallel and perpendicular to the channels, respectively. (D and E) The compressive stress-strain curve, , and micrographs present the bending-dominated failure of CPF-1-5 and the brittle cracking failure of CPF-5-5. The black containers in (E) show the injury induced by the exfoliation of little blocks earlier than the fracture appeared. (F and G) FEM simulations of thin- and thick-walled honeycomb constructions for the low- and high-density polymeric woods. The honeycomb constructions are coloured by the entire displacement of ingredient nodes. (F) Bending-dominated wall buckling of thin-walled honeycomb construction. (G) Cracking failure of thick-walled honeycomb construction.
Mobile supplies at all times exhibit excellent compressive performances alongside the channel course. The compressive efficiency of polymeric woods within the axial course is best than that of ceramic-based wood-like supplies comparable to SiC foams and mullite-zirconia foams in addition to the 3D-printed honeycombs (Fig. 3C). The broader density vary of the polymeric woods than different engineered wood-like supplies manifests a greater controllability within the microstructure; that's, the properties could be tuned by completely different preparation circumstances. Moreover, the polymeric woods are even akin to the pure woods in axial-direction compression (Fig. 3C). The elastic moduli of the polymeric woods are a lot greater than these of corks and the isotropous phenolic aerogels (fig. S17) (24, 25). The elastic moduli are akin to these of the mobile ceramic supplies however are decrease than these of pure woods. The oriented crystalline cellulose nanofibers (CNFs) within the pure woods are chargeable for the excessive stiffness. Different supplies with stochastic constructions comparable to resorcinol-formaldehyde resin (RF) aerogels and foams normally exhibit a steeper scaling of E ~ ρThree as a result of inefficient load switch and structural instability within the compression. In contrast, the scaling relationship (E ~ ρ1.6) of the polymeric woods manifests extra strong mobile construction and improved mechanical effectivity. The compressive property of the polymeric woods within the radial course can also be examined (fig. S18). The radial compressive strengths of the polymeric woods are a lot greater than these of the widespread pure woods (Fig. 3C). Moreover, the polymeric woods can adsorb modest impression power as a result of slight elasticity within the radial course, for instance, CPF-1 can recuperate from a 20% compressive pressure (fig. S18, D to F). Subsequently, polymeric woods will also be utilized in packaging and protecting padding to soak up the kinetic power with out producing intolerably excessive pressure on the protected object (26).
Throughout axial compression, the balsa wooden normally deforms by the cell wall’s plastic bending after which reaches densification (fig. S19). Within the axial compression of polymeric woods, we discovered two typical completely different failure modes, which rely on the resin (PF or MF) concentrations. The polymeric woods with comparatively low densities, comparable to CPF-1-5 and CMF-1-5, deform by gradual plastic bending of cell partitions and failure after reaching the yielding level (Fig. 3D, fig. S20, and flicks S2 and S3) (26). The polymeric woods with excessive densities, comparable to CPF-5-5 and CMF-2-5, current obvious brittle fracture behaviors with a drastic drop of stress and an instantaneous cleaving of the constructions (Fig. 3E, fig. S21, and flicks S4 and S5). Clearly, there's an inherent relationship between the failure modes and the structural options induced by the polymer focus within the preparation.
To make clear the 2 completely different failure eventualities, we carried out finite ingredient methodology (FEM) simulations to know the underlying deformation and injury mechanisms. Within the FEM simulations, common hexagonal hole columns (honeycomb construction; fig. S22) had been modeled to characterize the structural morphology of CPF and CMF specimens. As proven in Fig. 3F, the principle failure of the thin-walled honeycomb construction is as a result of bending-dominated buckling of skinny partitions (27), which is in good settlement with the compression experiment (fig. S20). It has been demonstrated that low polymer focus resulted in skinny partitions and enormous pores. Subsequently, compression straight precipitated bending and warping of skinny partitions close to the honeycomb opening (pleated floor within the experiments). To simulate the cracking failure of high-density polymeric woods, cohesive ingredient generated closed crackles preexisting on the middle of partitions alongside the size course. Through the compression experiments of high-density specimens, firstly of failure (earlier than the fracture appeared), the higher floor displayed injury with the exfoliation of little blocks (black containers in Fig. 3E). This course of led to the uneven contact floor (wall edges) within the compression. The exfoliation was primarily attributable to brittle thick-walled blocks and preparation-induced defects close to the contact floor. On this foundation, the mannequin was modified with projecting elements at two symmetric edges (fig. S23). The partitions with projecting elements appeared fractures in simulations, after which the cracking and additional compression resulted within the apparent lateral growth with lateral wall bending (Fig. 3G and fig. S23B). The mechanism of this cracking failure is just like that of the classical Brazilian check of a cylinder (28), through which the compression-induced tensile stress pulls the cross part after which lastly leads to the fracture. For the same mannequin with skinny partitions, the deformation remained the bending and buckling of skinny partitions with out wall cracking (fig. S24). Thus, the cracking failure mode must be attributed to the thick-walled honeycomb construction and the shaped uneven contact floor within the compression. As well as, FEM simulations revealed that bending existed in each failure modes, that's, bending-dominated thin-walled buckling and cracking-induced lateral thick-walled bending, respectively. The bending deformations within the two failure modes had been additionally in accordance with the scaling legal guidelines offered in Fig. 3B, demonstrating the bending-dominated plastic and cracking behaviors in structural failure. The perception obtained right here can be helpful for understanding the mechanical conduct of those wood-mimetic structural supplies.
The bending efficiency of the polymeric woods was additionally evaluated. The flexural strengths of the polymeric woods (for instance, CPF-5-5) bear comparability with these of the balsa woods. Nonetheless, as a result of inherent brittleness of thermoset resins, the polymeric woods (CPF-5-5) exhibit a slight toughness, with their flexural pressure a lot decrease than that of the pure balsa wooden (fig. S25). Contemplating the distinction between polymeric and balsa woods in construction and part, it's rational for the efficiency distinction. Impressed by the distinctive microstructure of the pure wooden, the toughness of the polymeric woods must be improved by compositing with biopolymers.
Corrosion resistance and thermal insulation
We then give attention to corrosion resistance and thermal conductivity of the polymeric woods, which ought to show some potential functions in particular environments. The pure woods have benefits in mechanical performances however normally endure from some drawbacks, such because the poor corrosion resistance below unconventional circumstances. Picket architectures can doubtlessly be destroyed by long-time corrosion of water as a result of hydrophilia of the wooden. To enhance corrosion resistance, pure woods are at all times lacquered or handled by plasma and corona to create water repellency (29), leading to excessive financial value and extra difficult remedy. Right here, corrosion resistance is an inherent benefit of the polymeric woods as a result of pure inertness of PF and MF resins. CPF and CMF polymeric woods show hydrophobic surfaces, with contact angles of 120 to 150° in each the axial and radial instructions, whereas balsa woods, with a contact angle of ~Zero°, rapidly adsorb water (fig. S26). After immersing the polymeric woods into the pure water (pH 7) and sulfuric acid answer (pH Three) for 30 days, the compressive strengths and moduli within the axial course scarcely lower (Fig. 4A), whereas the compressive strengths of the 2 sorts of balsa wooden (95 and 190 mg cm−Three) with the identical remedy lower to one-third of the unique strengths and the moduli concurrently lower to ~60% (fig. S27).
Fig. Four Corrosion resistance and thermal conductivities of polymeric woods.
(A) Axial compressive stress-strain curves of two typical polymeric woods earlier than and after immersing in water or acid answer for 30 days. (B) Thermal conductivities of balsa, industrial PF foam, and polymeric woods. (C) Schematic illustration displaying the distinction of thermal conductivity within the radial and axial instructions. (D) Thermal conductivity λ versus particular power for polymeric woods, conventional aerogel-like supplies, and different mobile ceramic supplies, together with polyurethane PU aerogels (38, 39), PF foams (40), nanocellulose aerogels (41), SiO2 aerogels (42), mobile CNF/GO/boric acid (BA)/sepiolite nanorods (SEP) aerogels (31), SiC foams (15), and mullite-ZrO2 aerogels (16). The polymer/SiO2 aerogels embrace pectin/SiO2 aerogels (43), cellulose/SiO2 aerogels (44), isocyanate/SiO2 aerogels (45, 46), and polyurethane/SiO2 aerogels (47).
Thermal conductivity can also be an necessary efficiency index in engineering materials analysis. In constructional engineering, picket constructions usually manifest a greater thermal insulation property than concrete constructions as a result of low thermal conductivity of wooden (30). The thermal conductivity of balsa wooden within the radial course is ~40 mW m−1 Ok−1, which is akin to the expanded polystyrene (35 to 45 mW m−1 Ok−1) and industrial PF foams (Fig. 4B) (31). Nonetheless, their functions within the thermal insulated supplies are extraordinarily restricted by hydroscopicity, which might result in the lowering thermal resistance as moisture content material will increase (32). In our experiments, the polymeric woods, with a density just like that of balsa woods (~90 mg cm−Three; for instance, CPF-1-5), can obtain higher thermal insulation with a thermal conductivity of 33 mW m−1 Ok−1 (Fig. 4B). As well as, compositing with nanomaterials into the cell partitions can improve the interface thermal resistance, which advantages thermal insulations (31). For instance, the CPF-1/GO-1 composite wooden exhibits a lowered thermal conductivity (28.9 mW m−1 Ok−1) in contrast with the pure CPF and CMF woods. We additionally discovered that the superinsulating composite wooden might be ready by additional decreasing the resol dosage. For instance, the CPF/GO composite wooden ready through the use of half resol dosage of CPF-1/GO-1 (denoted CPF-Zero.5/GO-1) manifests a radial thermal conductivity of solely 20.eight mW m−1 Ok−1, significantly decrease than that of the most typical superinsulating criterion (25 mW m−1 Ok−1) (Fig. 4B) (33).
The anisotropic construction with low density and excessive porosity was demonstrated to be useful to the thermal insulation (34, 35). 4 key traits are chargeable for the superior thermal insulation. First, the skinny partitions and enormous pore channels scale back the stable thermal conduction of the partitions within the radial course (perpendicular to the pore course). Second, the big pore channels (~50 μm) facilitate the anisotropic warmth movement alongside the pore course and scale back the proportion of the thermal conduction within the radial course (Fig. 4C). Third, the closed nanopores within the partitions, that are probably induced by polycondensation, might additional impede thermal conduction. Lastly, the nanomaterials (comparable to GO layers) not solely function thermal boundaries to decelerate the thermal transmission but in addition improve the interface, offering large interfacial thermal resistance and significantly lowering thermal conductivity (Fig. 4C) (31). Not too long ago, it has been proven that pure wooden–derived nanocellulose aerogels show an analogous thermal insulation property with a thermal conductivity of as little as 28 mW m−1 Ok−1 (34). Nonetheless, the nanosized spacing of the interfibril mixture within the cellulose partitions is principally open pores, displaying a restricted contribution to the thermal insulation within the radial course. Moreover, it's a problem to take care of low thermal conductivity for very long time as a result of excessive hydrophilia of CNFs.
Determine 4D exhibits polymeric woods, engineering supplies, and plenty of often used aerogel supplies within the airplane of thermal conductivity versus particular power. Their excellent thermal insulation and the superb mechanical efficiency place this new class of polymeric woods among the many state-of-the-art thermal insulators together with the polymer/SiO2 hybrid composite.
Hearth resistance of the polymeric woods
Inflammability is a deadly weak spot of pure wooden; thus, inorganic coatings are at all times used to enhance fireplace retardancy (36). Vertical burning check and limiting oxygen index (LOI) measurements had been carried out to look at fireplace retardancy of the polymeric woods (desk S2). The polymeric woods show excellent fireplace retardancy and self-extinguish rapidly when faraway from the igniting flame (fig. S28). The CPF/GO composite wooden ignites with issue, whereas the balsa wooden burned up rapidly in combustion exams (motion pictures S6 and S7). The light-weight CPF/SiC and CMF/SiC composite woods additionally burned as a result of the SiC nanofibers restrain shrinkage and the low density permits contact of the supplies with adequate oxygen. The polymeric and composite woods exhibit a considerably greater LOI worth than balsa wooden (21%) and different industrial, flame retardant–containing polymer foams (31). As an extension for additional doable functions, the efficiency of polymeric woods could be enhanced by compositing numerous nanomaterials, comparable to GO, SiC nanofibers, and sericite (Sc) nanosheets. Nanomaterials can inhibit shrinkage of the cryogels and lead to a comparatively slender density vary. The nanomaterials present nearly no impact on axial compressive power, however the compressive modulus is improved (fig. S29). The most important distinction between the composited wooden and pure wooden is oriented cellulose nanocrystal fibers alongside the pore course (37). As well as, each the matrix resin and the inorganic nanomaterials are arduous brittle supplies, which might end result within the untimely failure of the complete construction attributable to inadequate toughness. Whereas pure wooden is a composite of semirigid lignin glue and inflexible cellulose crystals, this pure “strengthened concrete construction” impressed us to hunt considerably versatile matrix supplies, for instance, polyurethane, amylopectin, sodium alginate, and different water-soluble resins. The versatile polymers and the oriented inflexible nanofibers alongside the pore course ought to yield excellent synthetic wooden.
MATERIALS AND METHODS
Fabrication of synthetic polymeric woods (CPF and CMF)
In a typical synthesis, Zero.60 g of phenol, 2.1 ml of formaldehyde answer (37 wt %), and 15 ml of (Zero.1 M) NaOH aqueous answer had been combined and stirred at 70°C for 1 hour. The pH of the sunshine yellow viscous answer was adjusted to impartial through the use of diluted HCl, and water was eliminated with rotary evaporators (50 mbar, 50°C). Absolute ethyl alcohol (60 ml) was added, after which the combination was filtrated to separate out the NaCl, adopted by evaporating the ethanol to acquire the low–molecular weight phenolic resol. The resol was saved in freezer. CTS (2 g) and HAc (2 ml) had been added to 100 ml of deionized water (DIW) below stirring to organize the clear and viscous CTS answer. Totally different plenty of the resol (Zero.11 to Zero.55 g) or MF (Zero.6 to 1.eight g) precursor had been added to three ml of the CTS answer, adopted by vibrating intensely and ultrasounding for five min. The fabrication particulars had been listed in desk S1. Then, the CTS/resin answer was poured right into a mould that was placed on a chilly copper platform and unidirectionally frozen. The preliminary temperature of the chilly platform was set to −10°C, and the freezing charge might be set to 1, 5, and 10°C min−1. After freeze-drying in a freeze drier (Labconco-195), the polymeric cryogel was cured at completely different temperatures, comparable to 160°, 180°, and 200°C.
Preparation and modification of varied nanomaterials
A Domsjö wooden pulp with a stable content material of ~30.Three% was used because the cellulose supply for the preparation of CNFs by TEMPO oxidation. Wooden pulp (Three.30 g; 1 g of dry cellulose) was suspended in 100 ml of water containing Zero.Zero16 g of two,2,6,6-tetramethylpiperidine-1-oxyl (TEMPO) and Zero.1 g of sodium bromide. Ten milliliters of 9% NaClO answer was adjusted to pH 10 by Zero.5 M HCl, which was then added to the wooden pulp suspension. The pH was maintained at 10 by including Zero.5 M NaOH till no NaOH consumption was noticed. The TEMPO-oxidized pulp was then rinsed a number of occasions with DIW and suspended in DIW to type a pulp slurry. The TEMPO-oxidized pulp slurry was agitated for five min to acquire a clear CNF dispersion.
The GO was ready based on the modified Hummers’ methodology. Briefly, 160 ml of sulfuric acid (98%) was added gently right into a beaker containing 5.Zero g of graphite and three.75 g of NaNOThree below stirring at room temperature. Subsequently, 20 g of KMnOFour was regularly added over 40 min, and stirring was stored for 20 hours. After incubation for six days, 500 ml of DIW was added slowly below mild agitation adopted by the addition of 30 ml of H2O2 (30%). The product was centrifugally washed and shocked for a number of occasions. Lastly, the brown dispersion was additional purified by dialysis to fully take away the impurities.
SiC nanofibers had been modified by coating a layer of RF by the Stöber methodology. The Sc nanosheets had been modified by coating a layer of polydopamine (PDA). In a typical synthesis, 50 mg of Sc and 50 mg of tris had been successively dissolved in 25 ml of DIW, and the pH was adjusted to eight.5 by diluted HCl. Dopamine hydrochloride (50 mg) was added to the above answer. After that, the answer was stirred for 12 hours in an open beaker. The obtained black Sc nanosheet was collected from the suspension by centrifugation and washed with water 3 times.
Fabrication of multifunctional composite woods
Totally different supplies, comparable to metallic ions [FeClThree, CoCl2, NiCl2, and Cr(NOThree)Three, Zero.2 mmol ml−1], SiO2 nanoparticles, CNFs, SiC@RF nanofiber, Sc@PDA nanosheets, and GO, had been added to the polymer answer. The focus of the nanomaterials might be 1, 5, and 10 mg ml−1. All of the composite woods are ready at a freezing charge of 5°C min−1, and the cryogels had been cured at 180°C.
For instance, the CPF-1/GO-1 composite wooden was fabricated as follows. In a typical synthesis, 2.Four g of CTS and a pair of.Four ml of HAc had been dispersed in 120 ml of GO answer (1 mg ml−1) below stirring and ultrasound for Three hours. Resol (Four.Four g) was added to the above combination answer below stirring to organize the PF/GO answer. The answer was poured right into a polydimethylsiloxane mould with an interior measurement of 5.6 cm × 5.6 cm × Four cm, which was placed on a precooled copper floor (−10°C). The answer was unidirectionally frozen at a freezing charge of 5°C min−1. The frozen monolith was freeze-dried for 72 hours after which cured at 180°C for 1 hour.
The do-it-yourself gear design and operation
To precisely management the freezing charge, a do-it-yourself gear was designed based on a earlier report (11). The gear consists of an automated liquid nitrogen tank, frozen ethanol pool, pattern stage (copper cylinder, diameter of 10 cm), and a temperature controller with a heating jacket wrapped the copper cylinder (fig. S4). Ethanol was used as a buffer of the liquid nitrogen attributable to its low melting level. The temperature controller can present the real-time temperature of the pattern stage, keep regular temperature, and management the freezing charge. Earlier than the pattern preparation, the temperature of the pattern stage was maintained at −10°C. After including the answer to the mould, the temperature of the pattern stage was managed to lower at a relentless charge. After the samples had been fully frozen, the mould was taken down and the samples had been taken out fastidiously. Word that any doable impression must be prevented, or else cracks will seem on the ultimate samples.
Mechanical compression exams and computational simulation
Mechanical compression and bending exams had been carried out on an Instron 5565A common testing machine outfitted with two flat-surface compression phases and 5000-N load cells. FEM simulations had been carried out with the ABAQUS program. The pattern measurement for the three-point bending check was 2 mm × 2 mm × 10 mm. The fundamental unit of the fashions was a daily hexagonal hole column with a uniform wall thickness. The honeycomb construction might be obtained by repeating the essential unit. We used the thin- and thick-walled fashions to simulate the ready supplies (CMF and CPF) with high and low matrix concentrations, respectively. Though the hole channels within the synthesized supplies had been irregular and inhomogeneous comparatively, the honeycomb mannequin might characterize the structural morphology from the attitude of theoretical simulation. In all simulations, the compression was realized by a inflexible airplane with a uniform displacement. The wall thickness of honeycomb constructions and the pore space are proven in fig. S11 and desk S1. Preexisting crackles on the middle of the partitions alongside the size course had been generated by cohesive components. The parameters of cohesive interface had been referred to the experiment information of bulk supplies. The low-density polymeric woods had been first simulated by the thin-walled honeycomb construction (fig. S22). The step size of the displacement of inflexible plate was Zero.001 in all simulations. The big deflection results had been included within the answer of compression processes. Then, we used the thick-walled mannequin with preexisting crackles (fig. S23) to simulate the high-density polymeric woods. Preexisting crackles had been generated by cohesive components. Due to our understanding of the cracking mechanism within the Brazilian check (28), we modified the thick-walled mannequin with projecting elements at two symmetric edges. The same thin-walled mannequin was additionally simulated as a comparability (fig. S24). In FEM simulations, C3D8R and COH3D8 components had been chosen for the partitions and cohesive interfaces, respectively. Due to the constraints of computational value and time, the meshing grids in thick-walled fashions with preexisting crackles had been bigger than these in thin-walled fashions. The wall thicknesses of the 2 fashions had been 2.Zero and 6.6 μm, respectively, and the facet size of the hexagonal opening in each two fashions was 21 μm.
Characterization
SEM was carried out with a discipline emission scanning electron microanalyzer (Zeiss Supra 40). All samples had been gold-sputtered for 50 s at a relentless present of 30 mA earlier than commentary. TEM was carried out on H-7650 (Hitachi) working at an acceleration voltage of 100 kV. The x-ray microtomography was performed on Y.Cheetah (YXLON) for the 3D microstructural info. The uncooked information had been reconstructed utilizing the software program VGStudio MAX 2.2 by assembling the static pictures in sequence. The skeletal densities of CPF and CMF had been 1.Three ± Zero.1 and 1 ± Zero.1 g cm−Three, respectively, based on the pycnometer methodology. The in-site commentary of the compressive strategy of polymeric woods was recorded with a monocular microscope (JT-1400B). The thermal conductivity was measured utilizing the transient airplane supply approach. The vertical check was carried out on a CFZ-2 sort instrument (Jiangning Evaluation Instrument Co.) based on the UL 94 check commonplace. The specimens used had been of dimensions 130 mm × 13 mm × Three mm. LOI was measured based on ASTM D2863. The equipment used was an HC-2 oxygen index meter (Jiangning Evaluation Instrument Co.). The specimens used for the check had been of dimensions 100 mm × 6.5 mm × Three mm.
Corrosion resistance exams
CPF-Four-5, CMF-2-5, and balsa with a measurement of 1.5 cm × 1.5 cm × 1.5 cm had been put in a beaker with pure water. The samples had been floated spontaneously on the water floor and stored for 30 days. In one other beaker, diluted sulfuric acid (pH Three) was used to look at the corrosion resistance of polymeric and balsa woods. No less than three samples had been examined for each pattern. Then, the compressive performances of those woods had been examined.
SUPPLEMENTARY MATERIALS
Supplementary materials for this text is out there at http://advances.sciencemag.org/cgi/content material/full/Four/eight/eaat7223/DC1
Fig. S1. The chemical constructions of matrix supplies.
Fig. S2. SEM pictures of varied MF-based composite woods.
Fig. S3. Giant-scale fabrication of the polymeric wooden.
Fig. S4. Pictures of the do-it-yourself gear to manage the freezing charge.
Fig. S5. SEM pictures displaying the altering development of the microstructures of CPF woods with the rising resol content material and freezing charge, respectively.
Fig. S6. Statistical evaluation of space distribution of the channels of CPF woods ready at completely different freezing charges.
Fig. S7. Statistical evaluation of wall thickness.
Fig. S8. SEM pictures displaying the altering development of the microstructures of CPF woods with the rising resol content material and curing temperature, respectively.
Fig. S9. Statistical evaluation of space distribution of the channels of CPF woods ready through the use of completely different curing temperatures.
Fig. S10. Statistical evaluation of wall thickness.
Fig. S11. The averaged pore space and averaged wall thickness of CPF woods.
Fig. S12. SEM pictures of the CMF woods.
Fig. S13. Densities and porosities of the polymeric woods.
Fig. S14. The mechanical performances of CPF woods ready at completely different freezing charges.
Fig. S15. The mechanical performances of CPF woods ready at completely different curing temperatures.
Fig. S16. The mechanical performances of CMF woods ready at completely different freezing charges.
Fig. S17. An Ashby chart plotting compressive stiffness versus density for CPF and CMF woods.
Fig. S18. The radial compression exams of balsa, CPF, and CMF woods.
Fig. S19. The axial compression of the balsa wooden.
Fig. S20. The in situ micrographs present the failure of polymeric woods with comparatively low density.
Fig. S21. The in situ micrographs present the failure of various polymeric woods with comparatively excessive density.
Fig. S22. Skinny-walled mannequin for the compression simulations of low-density polymeric woods.
Fig. S23. The simulation fashions and outcomes.
Fig. S24. An identical thin-walled mannequin was additionally simulated as a comparability.
Fig. S25. Three-point bending check of balsa woods, polymeric woods, and a typical composite wooden.
Fig. S26. The contact angles of the everyday polymeric woods.
Fig. S27. The water resistance of balsa woods.
Fig. S28. The hearth resistance of polymeric woods and balsa wooden below an alcohol flame.
Fig. S29. The contrasts of CMF woods with numerous CMF-based composite woods in mechanical efficiency.
Desk S1. The main points of the synthesis of typical CPF and CMF woods and their respective parameters.
Desk S2. Vertical burning check and LOI of the balsa (~300 mg cm−Three) and polymeric woods.
Film S1. 3D commentary of a typical CPF wooden by x-ray microtomography.
Film S2. The in situ commentary of failure strategy of the low-density CPF-1-5 in the course of the compression, revealing the gradual plastic bending of cell partitions.
Film S3. The in situ commentary of failure strategy of the low-density CMF-1-5 in the course of the compression, revealing the gradual plastic bending of cell partitions.
Film S4. The in situ commentary of failure strategy of the high-density CPF-5-5 in the course of the compression, revealing the brittle fracture behaviors.
Film S5. The in situ commentary of failure strategy of the high-density CMF-2-5 in the course of the compression, revealing the brittle fracture behaviors.
Film S6. The burning check of the CPF-1/GO-1 composite wooden through the use of an alcohol lamp flame.
Film S7. The burning check of the balsa wooden through the use of an alcohol lamp flame.
Acknowledgments: Funding: This work was supported by the Nationwide Pure Science Basis of China (grants 51732011 and 11525211), the Basis for Modern Analysis Teams of the Nationwide Pure Science Basis of China (grant 21521001), Key Analysis Program of Frontier Sciences, Chinese language Academy of Sciences (grant QYZDJ-SSW-SLH036), the Strategic Precedence Analysis Program of the Chinese language Academy of Sciences (XDB22040402), the Nationwide Fundamental Analysis Program of China (grant 2014CB931800), the Elementary Analysis Funds for the Central Universities (WK2090050040), and the Customers with Excellence and Scientific Analysis Grant of Hefei Science Heart of Chinese language Academy of Sciences (2015HSC-UE007). Z.-L.Y. acknowledges the funding assist from the Nationwide Postdoctoral Program for Modern Skills (grant BX201700220) and the China Postdoctoral Science Basis (2017M622017). Y.-B.Z. acknowledges the funding assist from the Nationwide Postdoctoral Program for Modern Skills (grant BX201700225). This work was partially carried out on the College of Science and Expertise of China Heart for Micro and Nanoscale Analysis and Fabrication. Creator contributions: S.-H.Y., Z.-L.Y., and N.Y. designed the experiments. Z.-L.Y., N.Y., Z.-Y.M., and B.Q. carried out the artificial experiment and evaluation. T.M. and S.-C.L. helped within the synthesis of the composite woods. L.-C.Z., Y.-B.Z., and H.-A.W. processed the FEM simulations and mechanical evaluation. Y.-Y.L. and H.-L.G. performed the 3D reconstruction of the construction. W.-Y.X. carried out the fire-retardant experiments. S.-H.Y. and Z.-L.Y. wrote the paper. All authors mentioned the outcomes and commented on the manuscript. Competing pursuits: The authors declare that they don't have any competing pursuits. Information and supplies availability: All information wanted to guage the conclusions within the paper are current within the paper and/or the Supplementary Supplies. Extra information associated to this paper could also be requested from the authors.
Tecriter,2018-8-10,https://tecriter.com/bioinspired-polymeric-woods-science-advances/